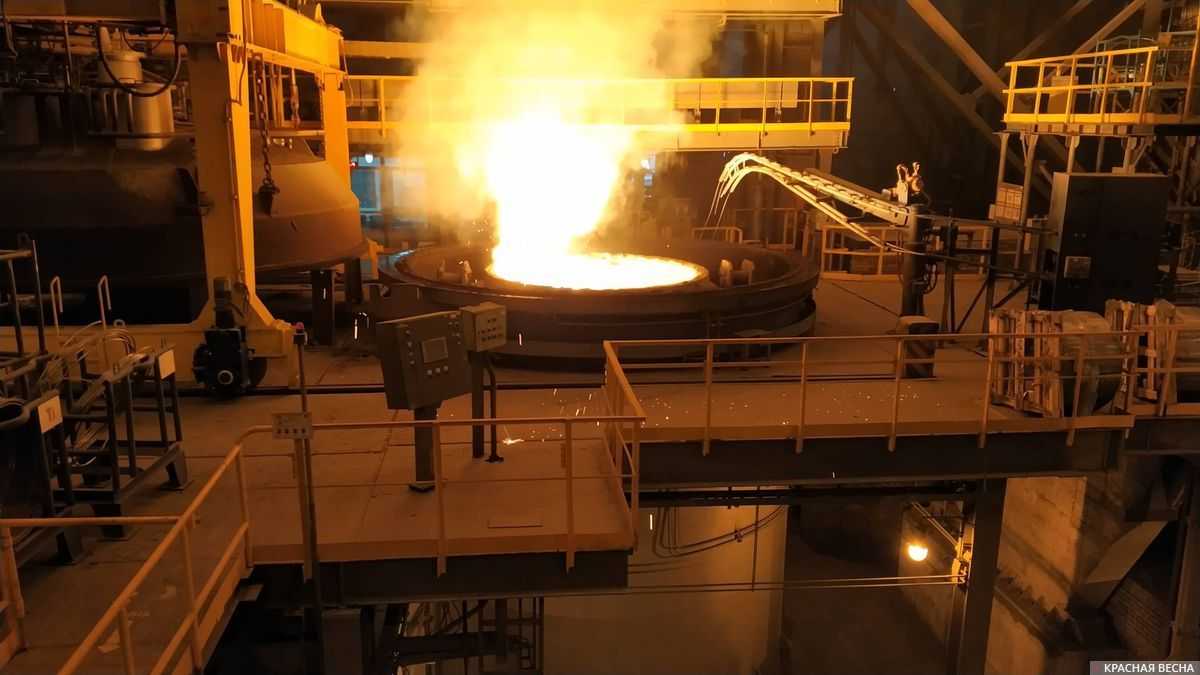
Технологию получения сиалона (оксидонитритной керамики) путем азотирования в режиме горения (методом СВС) разрабатывают ученые Томского научного центра (ТНЦ) СО РАН, 25 сентября сообщает пресс-служба ТНЦ.
Сиалоновые фильтры в настоящее время широко востребованы в металлургической промышленности, так как они позволяют в расплавах металлов улавливать различные включения, повышая тем самым качество отливок.
На металлургических предприятиях России сейчас используют сиалоновые керамические пористые фильтры расплава производства западных стран. Они очень дороги, так как их получают традиционными способами, требующими многодневной обработки изделий при очень высоких температурах.
Руководитель проекта, научный сотрудник лаборатории новых металлургических процессов Антон Регер рассказал о новой технологии производства сиалона:
«Преимущества СВС-азотирования заключаются в его быстроте, простом оборудовании и энергоэффективности. Производить сиалон таким методом предложили еще 30 лет назад, но долгое время методом СВС удавалось получать лишь бесформенные спеки керамики, требующие измельчения в порошки для последующего создания изделий на их основе. Поэтому сегодня нет сомнений в актуальности передовой технологии получения уже готовых к использованию в промышленности пористых керамических изделий, не нуждающихся в дополнительной механической или термической обработке».
На первом этапе проекта ученые определят оптимальные составы, позволяющие в результате химических реакций между кремнием, алюминием, оксидом кремния и азотом получить чистый порошок сиалона без посторонних примесей.
Далее они определят предварительную структуру порошковой заготовки. Для получения нужной структуры будущего изделия создается специальная жидкая масса — шликер. Он состоит из сиалоновой порошковой смеси, водно-щелочного раствора, определяющего размер пор будущего изделия, жидкого стекла, придающего прочность и фиброволокна, армирующего пористый каркас заготовки.
При взаимодействии водно-щелочного раствора с исходной порошковой смесью, в которой содержится алюминий и кремний, выделяется газ, формирующий поры. В конечном итоге создается хрупкий «скелет» заготовки. Его осторожно извлекают из формы и сушат.
На следующем этапе в специальном реакторе выполняется СВС-азотирование, в процессе которого происходит горение при температуре от 1600 до 1800 ℃, и «скелет» заготовки становится готовым изделием с необходимыми физико-химическими свойствами.
Для того чтобы изделие действительно соответствовало заданным характеристикам, должны быть определены и выдержаны оптимальный состав порошковой смеси и условия азотирования в режиме горения. Поскольку процессы в СВС протекают очень быстро и в агрессивных условиях, могут возникать трещины.
Для определения этих оптимальных условий ученые в лабораторном реакторе сначала получат для исследования образцы кубической формы 8×8 см, а затем уже в полупромышленном реакторе — образцы более крупного размера.
Другой важной задачей исследования является подбор оптимального размера и формы пор материала. Руководитель проекта подчеркнул, что от характеристик пористости фильтра зависит эффективность очистки расплавов металлов. Поэтому в ходе исследований ученые выявят влияние составов шликера на размер пор готового изделия.
glavno.smi.today
Все новости:
glavno.smi.today
45894